Kudos Blends has recently completed a significant upgrade to its Mill Line production facility, marking a key milestone in our drive for increased efficiency, improved safety, and future-proofing our operations.
The project, which was undertaken over March and April 2025, saw the installation of new equipment and a complete rethinking of the mill layout. This is now fully operational and proving to be a huge improvement.
Key Upgrades
Several critical changes were made as part of this project, including:
- Installation of a new 5000-litre storage hopper that allows continuous production without the need for stop-start operations. This significantly reduces forklift truck movements, improving workflow and safety.
- A larger blender/mixer which enables bigger batch sizes, easing the manual handling workload for production and warehouse teams.
- A new PLC (Programmable Logic Controller) screen with an intuitive interface, allowing operators better visibility and easier control of the process.
- Additional equipment such as a new conveyor, rip & tip station with built-in extraction, lump breaker, slide valve, and rotary valve to enhance processing and reduce dust.
A More Efficient and Safer Process
Prior to the update, frequent interruptions were required to move intermediate bulk containers (IBCs), creating inefficiencies, bottlenecks, and dust-related issues. The mill’s older control systems also posed challenges in reliability and flexibility.
Matt Norris, Operations Support, and a previous production operative, was significantly involved in the project implementation. He explains, “It’s a great improvement and is just going to make everything a lot easier for the production staff. The work won’t be as tiring. Less stop-start means more efficiency, and more efficiency means we can deliver more product, faster and to a higher standard.”
Now, with a fully enclosed system and streamlined layout, the need to manually move bins and IBCs between the mill and packing areas has been eliminated.
Tilly Little, Head of Production, has seen a significant improvement: “Everyone is really excited to be working with the new system and the orders are flying through. No more obstacles in the way of the fork lift trucks…the factory looks great – clean, neat, tidy & organised!“
This work not only simplifies operations but also improves health and safety conditions significantly.
“The mill upgrade project will significantly improve safety in our food production facility”, explains Nick Jones, Head of Health and Safety. “We are reducing transport movements, decreasing workplace exposure, increasing efficiencies, lessening manual handling tasks and making workers safer”.
Supporting Long-Term Goals
This upgrade supports Kudos Blends’ broader strategic aims, including increased production capacity and alignment with KODA™ targets. By enabling a more continuous, automated process, the improvements also future-proof the facility for potential expansion and customer demand growth.
Director Dinnie Jordan explains,“This project was about more than just new equipment—it supports our growth, improves working conditions, and builds a stronger future for our production team and our customers.”
Team Collaboration and Execution
The project was executed on schedule thanks to a well-coordinated effort between Kudos Blends’ internal team and external partners, including WBT Services and Unitrak Powderflight.
Special recognition goes to Mark Thompson from WBT, whose meticulous planning and commitment helped ensure smooth delivery despite logistical challenges, such as manoeuvring large equipment through some tight spaces!
Looking Ahead
While the team is satisfied with the current enhancements, the company is always open to further development across departments. This year has also seen a brand-new custom bakery, and a state-of-the-art laboratory upgrade, as well as continued Health & Safety and Workplace transport improvements.
This Mill Line upgrade represents a bold step forward, reinforcing Kudos Blends’ commitment to innovation, efficiency, and creating a safer, smarter working environment.
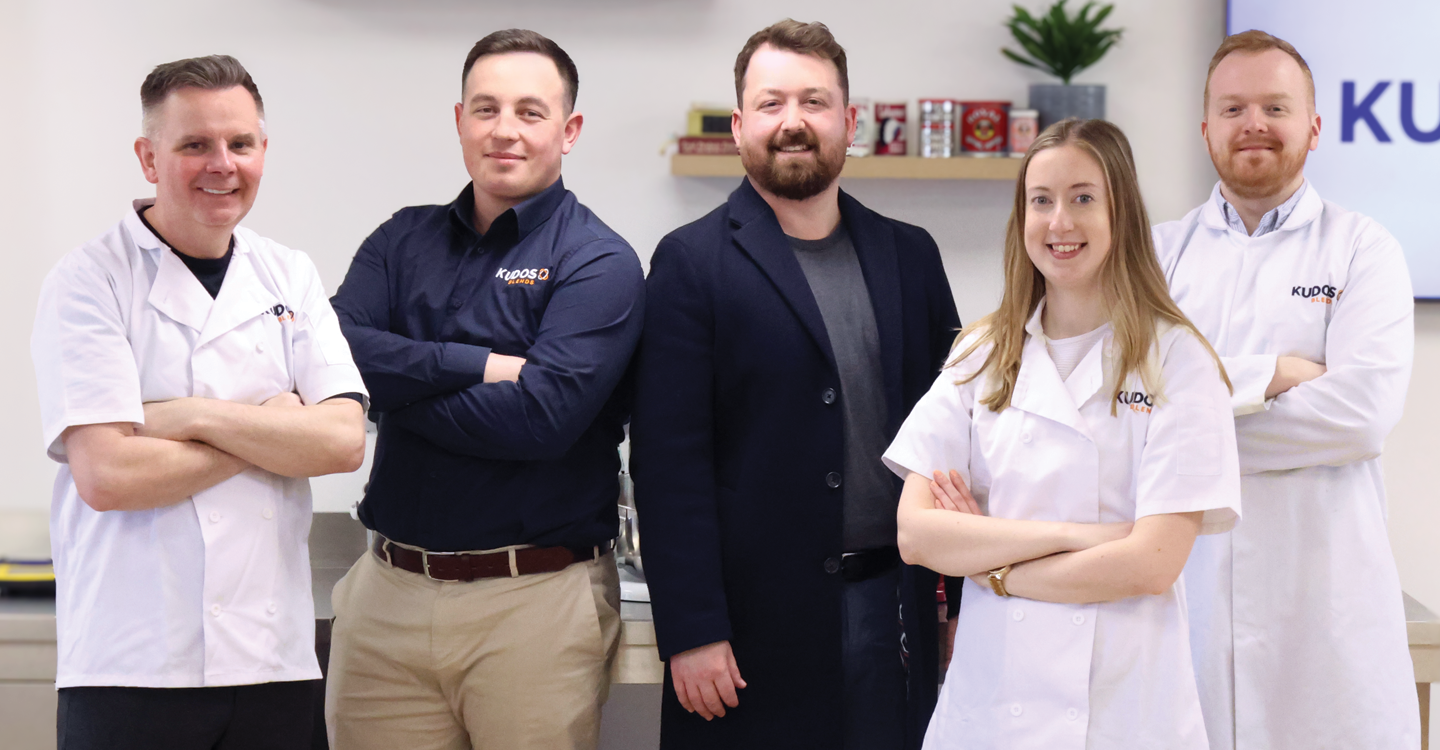