From AI software to baking powder, it holds true that the quality of an output is largely determined by the quality of the input. Raw material testing is undertaken in an array of industries including pharmaceuticals, food manufacturing and construction. Different materials, different test methods, and different results all carried out with the same goal in mind; maintaining the highest quality and safety standards in the finished product.
Elevating Standards
The final product for us is something we want to be exceedingly confident about; this is why we are dedicated to testing our raw materials thoroughly. For this reason, we have an in-depth approval process for any new raw materials including a range of chemical and physical analyses to assess whether the material is suitable for use in our blends from a safety, functionality and legality perspective. A single snapshot is not always fully representative and that is why it is important to continue analysing incoming raw material shipments long after the first sample is received.
Another aspect of why we are steadfast to test in this method is because we are a time-critical company. Our plan to order raw materials in high volume with a conscientious approach allows us to not get caught in a situation where we are haphazardly and chaotically sourcing with a last-minute outlook.
This approach allows us to make adjustments in a timely manner rather than panic when a raw material has not met the required specification.
As a result, this level of testing sets us apart; the strictness and the consistent nature of our analysis, gives us the confidence that our raw materials are of the uppermost standard.
How We Work
At the start of each year, we set out a month-by-month breakdown of which ingredients will be tested. The frequency with which each material is tested relies on a number of factors, including quantity used, length of time the supplier has been used, and country of origin . The panel of tests carried out on each material is decided based on review of both the purity specifications outlined by law and the specifications provided by our suppliers.
On top of this, we often carry out additional tests that can provide further information and clarity to our customers that the quality of our raw materials is of a high standard.
Furthermore, if a certain raw material cannot be tested in-house, we will also use UKAS accredited laboratories to certify that the raw materials are of the required standard.
The importance of testing raw materials is sometimes overlooked by manufacturers and we have found that certain companies choose to rely solely on the CoA (certificate of analysis) from their suppliers. When the quality of these raw materials can dictate the functionality and stability, even the shelf-life of the final product This apathy towards testing can lead to a variety of issues in the future.
The time-consuming nature of having a raw material which isn’t up to specification can cost in several ways; monetarily, occupation of warehouse space, and the lost time of your team. This has the potential of having a seismic effect on day-to-day operations which can take weeks to recover from. With the time constraints that we can have, we see this as an opportunity to thwart the unexpected.
A downside to this approach is the cost attached to testing raw materials consistently and the aspects which align with this; laboratory, laboratory employees, the testing capabilities et al. The time consumed by the constant testing and the monetary outlay are all factors which need considering when deciding the extent of testing that is suitable.
Personal Touch
The reason why we test in such a robust way is to iron out any of the kinks that can arise. In instances where material has been delivered out of specification such as when a supplier changes their manufacturing process -our stringent policy has allowed us to avoid contaminating tonnes of our baking powders due to the testing which we do scrupulously. The total associated with such a blunder could be disastrous which is why we are happy to incur the cost of testing as consistently as we do.
With baking powder playing such an important role in a huge amount of bakery products, slight process deviations can compound into non-conformances further downstream resulting in product wastage and unhappy customers. We believe wholeheartedly that testing is a necessity as one of the world’s leading leavening agent manufacturers, this is one of the small reasons why we are Grade AA+ certified from BRC. We’ll leave you with a little something to ponder:
The best chefs do not only taste their food after it is served, they do so at every available step along the way. When your ingredients are a variety of powders and you cannot taste, you test!
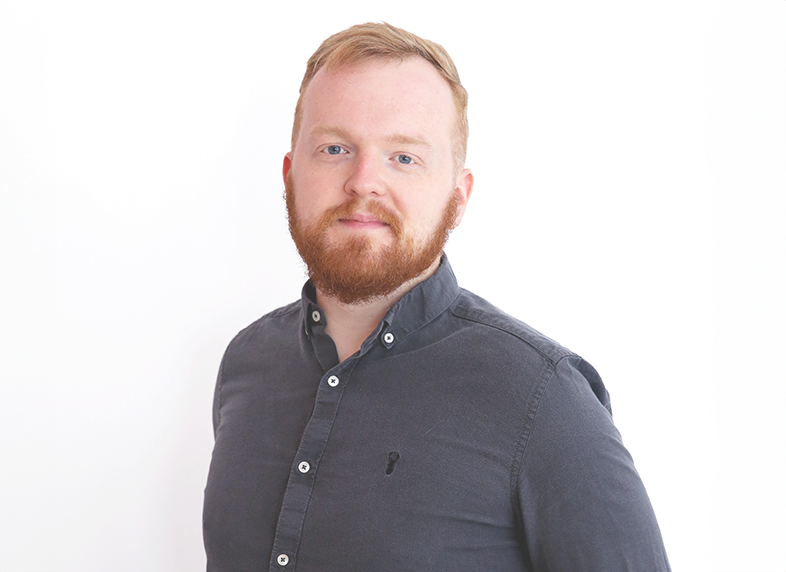